In preparation for the upcoming Pharmapack conference in Paris, we are spotlighting one of our working groups at the Alliance to Zero which has been working on an innovative and collaborative project reducing plastic packaging in pre-filled syringes.
We interviewed Nadine Lampka, Lidia Smith and Christoph Zauner from Schreiner MediPharm, Körber and SCHOTT Pharma on collaborating to create secure blister-free syringe packaging.
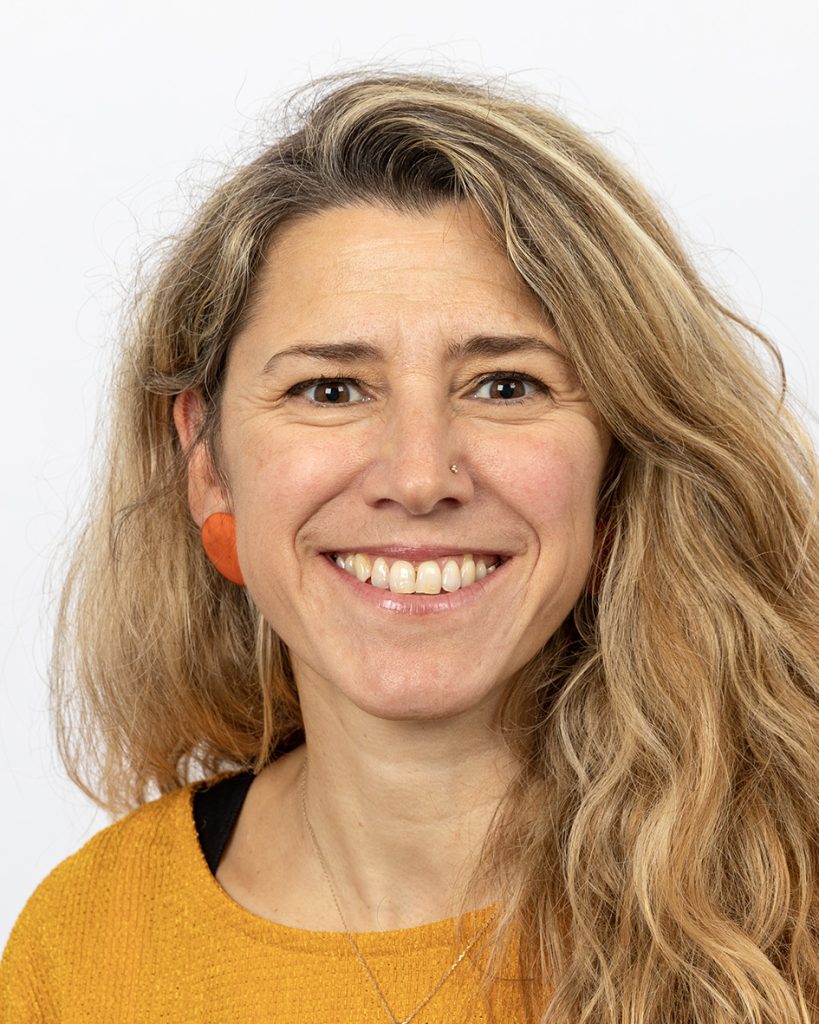
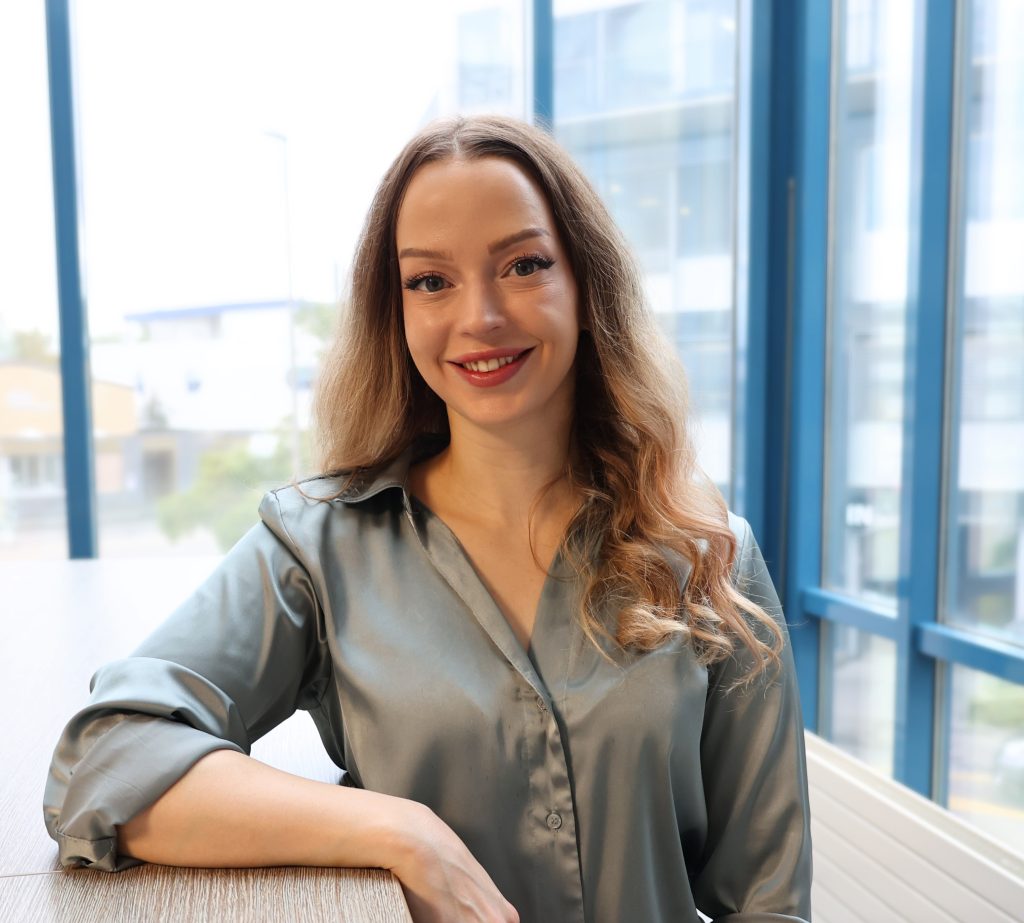
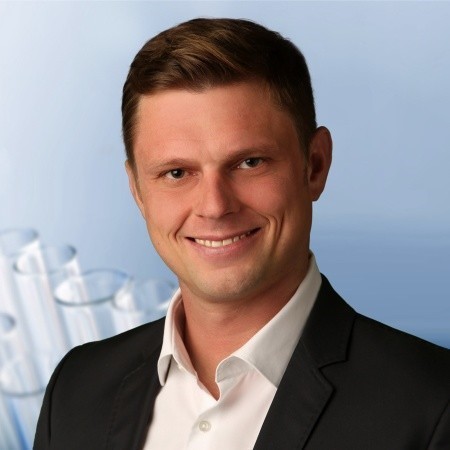
How did the secure blister-free syringe project originate?
Nadine: At Schreiner MediPharm we have been discussing secure blister-free packaging since working on a new label concept that allows for first-opening indication on syringes, a crucial functionality to take over from the blister pack. The Alliance to Zero has facilitated the cross-industry collaboration with SCHOTT and Körber, working together to provide a pre-tested holistic solution to the industry; SCHOTT’s COC syringe, Schreiner MediPharm’s functional label and Körber’s packaging boxes.
Lidia: To minimize environmental impact and maximize efficiency, we need to question and revolutionize traditional packaging methods. Blister packaging, while once ubiquitous, poses significant challenges in terms of waste generation and logistical complexity.
Christoph: We wanted to create a solution which still had the benefits of blistered packaging such as first-opening indication, protection from mechanical stress, contamination and in some cases, oxygen or UV protection.
Nadine: Rather than replacing the blister with a recycled material option, we are going one step further and removing the plastic component completely. Crucially, we are still fulfilling the key functionalities of the blister packaging and can even offer more benefits.
What is the new solution you have created? What are the key functionalities of each component?
Christoph: The solution starts with the syringe. We’ve created a new cap design for different syringe volumes, which have an equal circumference of cap and syringe. The syringe comes ready-to-fill with no cap assembly needed.
Nadine: This new cap design enables labelling all the way up to the cap closure, and this is where Schreiner MediPharm’s functional label comes in. The label provides ideal protection against tampering and contamination. The irreversible first-opening indication seals the primary packaging until point of use. This first-opening indication can be analog or digital (RFID). As well as security, the label can also provide additional functionality such as UV/light or gas protection.
Lidia: The syringes then go directly into Körber’s carton box designed for high product protection and top-loaded for product accessibility. Körber uses their NeoTop X to print and package, and the product is volume optimised and made of 100% mono-material paperboard.
What are the key benefits of the secure blister-free packaging concept?
Lidia: The secure blister-free packaging saves ~25% in packaging dimensions. The higher density packaging has the benefits of reducing transport weight and volume, and therefore reducing the carbon footprint and logistics costs. We calculated for a 5ml SCHOTT TOPPAC® syringe, a palette would fit 6300 syringes, versus 5040 syringes in traditional blistered packaging. Scaled up, this would be 16 fewer containers needed for a shipment of 10 million syringes.
Christoph: The solution is sustainable by design with 80% less plastic and packaging waste created. Using Lidia’s example case of 10 million syringes travelling from Hamburg to New York, we would have accumulated a total of 87.400 kg CO2e, made up of 68.200 kg CO2e of saving from the removal of plastic components and 19.200 kg CO2e saved from the logistics of reduced volume and weight. This is the equivalent of 14 round-the-world flights.
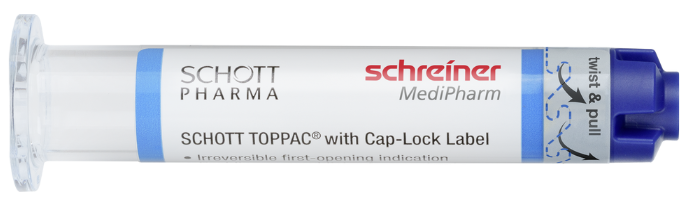
Nadine: There are also further benefits along the value chain. Three times less storage space is needed in transportation and distribution but also in hospital refrigerators or Pyxis cabinets. With the first-opening indication, it is clear if a product has been opened or used. This new approach is also in line with the ISO-EN 21976, and can add a digital indication for traceability by RFID. Studies have also shown pre-filled syringes can increase patient safety by reducing medication errors and saving time in administering the drug.
How does the secure blister-free syringe project align with the Alliance’s vision for the future? How has the Alliance helped this project to develop?
Lidia: The Alliance aims to facilitate the transition of the supply chain for the pharma and biotech sector to compliance with net zero emissions in line with the goal of the Paris Climate Agreement. Product packaging design is a key lever to support a sustainable supply chain and to help pave the way to net zero. Blistering is an energy intensive process and, as outlined earlier, we can save substantial carbon emissions going blister-free.
Nadine: We’ve been able to leverage the Alliance to gain understanding across our stakeholders and the wider industry. Pooling our resources and networks has been useful and definitely sped up the development process to create a tangible solution.
What has been a highlight of the project so far?
Christoph: The shipping study was an important milestone for us. We pre-tested the solution in a ISTA 3A shipping study, which passed with no breakage, leakages and the tamper-evident seal was still intact.
Nadine: For me, the intersection between security and sustainability is key. The first-opening indication seal is crucial to the functionality and has allowed us to remove the blister while still providing product and patient safety.
Lidia: I think this project shows the high impact you can achieve in collaboration. Individual companies are limited in their scope and working together across primary and secondary packaging partners has created a holistic solution we couldn’t have achieved alone.
How do you imagine the project will evolve? How could other value chains learn from your process in the project?
Nadine: The aim of our project is to provide a sustainable, tangible solution to the pharmaceutical industry and healthcare professionals that helps reducing waste, carbon footprint, cost and increases security, patient safety and product convenience. This concept can be used for many different types of syringes, and the underlying concept can be used across the industry in all blistered packaging.
Christoph: Now some key relationships are in place, we can look at solving the next problem together. We need to be open in the pharmaceutical industry and share the challenges and barriers we are facing when it comes to sustainability. This transparency and awareness can then lead to development of a solution.
We are excited to launch the secure blister-free syringe packaging solution at Pharmapack and will have an interactive workshop on Thursday January 23rd from 10:10-11:25 am, alongside Philipp Ludihuser of SCHOTT Pharma.
